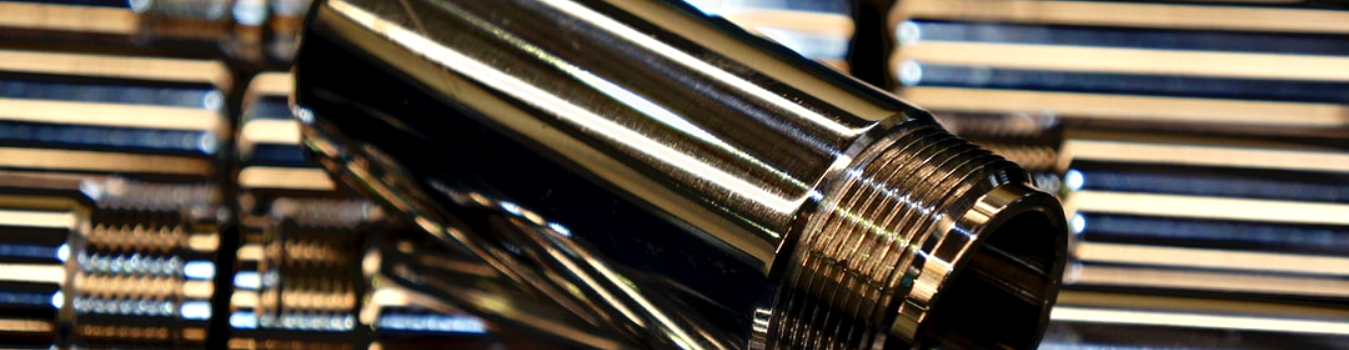
E-coating is a popular method used in several industries including aerospace, agriculture, vehicle manufacturing, and jewellery business. E-coating, known as electrophoretic coating process or electropainting, involves the usage of electric current to apply a coat of painting over metals and other materials. E-coating is somewhat similar to that of electroplating – both processes involve a fluid bath to ensure the consistency of the coating. A process that developed in the 1950s and 60s, now it has high demands and widespread application.
Processes Involved in E-Coating
There are many processes involved when it comes to e-coating. The overall result of the process is to coat a material with a protective coating that will keep the material resistant to a variety of corrodents.
In e-coating, a component is submerged into a bath where with the help of the passage of electric current, the component is coated with paint or any other protective layer. The four major steps involved in this process are – pretreatment, coating in an electric bath, post-rinsing, and baking in an oven to attain a smooth finish.
Benefits of E-Coating
E-coating is a very popular method that is practised across a wide range of industries because it boasts several advantages.
- Efficient-The electrophoretic process is efficient as there is almost no wastage in this process, compared to other coating methods. When used in higher volumes, this process is very handy and ensures a profitable result.
- Highly Durable –Â E-coating can endure harsh wear and tear and still remain good as new. It can withstand environmental hazards and is chip resistant. This is the reason why this process is used in industries like the aerospace industry.
- Consistent Finish –Â One admirable quality when it comes to the process of electrophoresis is that it allows the consistent application of the coating to a component. By adjusting the current flowing through the fluid bath, one can determine the thickness of the coating.
- Complete Coverage –Â Be it complex machinery parts or intricate jewellery, anything can be completely coated with the help of e-coating.
- Environment-friendly –Â As the e-coating process is based on water-based immersion technology, there is not much risk for the release of hazardous wastes and compounds.
Electro less nickel (EN) plating is a chemical reduction process which depends upon the catalytic reduction process of nickel ions in an aqueous Process (containing a chemical reducing agent) and the subsequent deposition of nickel metal without the use of electrical energy. Due to its exceptional corrosion resistance and high hardness, the process finds wide application on items such as valves, pump parts etc., to enhance the life of components exposed to severe conditions of service, particularly in the oil field and marine sector. With correct pretreatment sequence and accurate process control, good adhesion and excellent service performance can be obtained from EN deposited on a multitude of metallic and non-metallic substrates.There are four commonly used methods of applying e-Coating to steel surfaces. These are hot-dip galvanizing, thermal spraying, electroplating and sherardizing.
In the EN plating process, the driving force for the reduction of nickel metal ions and their deposition is supplied by a chemical reducing agent in Process. This driving potential is essentially constant at all points of the surface of the component, provided the agitation is sufficient to ensure a uniform concentration of metal ions and reducing agents. Electro less deposits are therefore very uniform in thickness all over the parts shape and size. This process offers distinct advantages when plating irregularly shaped objects, holes, recesses, internal surfaces, valves or threaded parts. Distinct advantages of EN plating are: Uniformity of the deposits, even on complex shapes.
- Deposits are often less porous and thus provide better barrier corrosion protection to steel substrates, much superior to that of electroplated nickel and hard chrome
- The deposits cause about 1/5th as much hydrogen absorption as electrolytic nickel and about 1/10th as much hard chrome.
- Deposits can be plated with zero or compressive stress.
- Deposits have inherent lubricity and non-galling characteristics, unlike electrolytic nickel.
- Deposits have good wet ability for oils
Why Choose Our E-Coating Services?
At Jay Ambay, we ensure the perfection of every component we process. Our e-coating methods are scientifically validated – our state-of-the-art facilities make us one of the pioneers in this industry.
- Expertise –Â At Jay Ambay, we employ skilled professionals who have been working in this field for several years. With their expert touch, we refine our methodologies and strive to deliver the best.
- High-quality Output –Â Our coating services have proven to be excellent – with us, your components attain the fine finish they need.
- Skillful Handling of High Volumes –Be it a project of any quantity, we are equipped to undertake it at Jay Ambay and work on it with meticulous attention.
- Customer-friendly –Â We serve to please, so you can put your requests forward with us regarding your project and we will do our best to accommodate your requests.
Frequently Asked Questions?
 E-coating, also known as electrodeposition coating or electrocoating, is a method of applying a protective and decorative finish to various objects. It involves immersing the object in a water-based paint bath and applying an electric current to deposit the coating onto the surface.
E-coating uses an electric current to attract and deposit paint particles onto the object’s surface. The object acts as the cathode, while the paint bath contains the anode. The electric current causes the paint particles to adhere to the surface, forming a continuous and uniform coating.
E-coating can be applied to a wide range of materials, including metals like steel, aluminum, iron, and zinc, as well as certain plastics and composites. It is commonly used in industries such as automotive, appliances, furniture, construction, and aerospace.
Yes, E-coating is considered an environmentally friendly coating process. It uses water-based paints, which have lower VOC emissions compared to solvent-based coatings. Additionally, E-coating generates minimal waste, as excess paint from the process can be easily reclaimed and reused.
Absolutely! Excellube EC10 can be top coated with a variety of powder coatings even if it contains PTFE. This has the advantage that e-coat completely covers a part, even in complicated places where powder coating can’t. Furthermore, the coating thickness is managed, making it unnecessary to worry about coating dimensionally delicate sections like threads.
The pieces offer even greater corrosion resistance and a larger range of hues after being top coated with powder. Of course, everything depends on how well the e-coat application was done. We at EMC have extensive experience applying e-coat across several industries and have done so for a long time. You may be guaranteed to receive the best service possible because to our unparalleled experience.